Prismatic Cell Production Line: Streamlining Battery Manufacturing
A prismatic cell production line is an integrated system designed for the efficient manufacturing of prismatic lithium-ion battery cells. These cells are favored in applications such as electric vehicles (EVs) and energy storage systems due to their compact design and high energy density. The production line encompasses various stages, from material preparation to final testing, ensuring that each cell meets quality and performance standards.
● Key Stages in a Li Ion Battery Making Machine
1. Material Preparation
- Electrode Materials: Active materials for anodes (typically graphite) and cathodes (often lithium metal oxides) are prepared and mixed with binders and conductive additives.
- Separator Production: Separators, which prevent electrical short circuits between the anode and cathode, are fabricated from porous materials like polyethylene or polypropylene.
2. Electrode Fabrication
- Coating: The electrode slurry is uniformly coated onto metal foils (aluminum for cathodes and copper for anodes) using advanced coating machines. This process is crucial for achieving the desired thickness and uniformity.
- Drying: Coated electrodes are dried in controlled environments to remove solvents and enhance electrochemical performance.
- Calendering: The dried electrodes are compressed to increase density and improve electrical conductivity.
3. Cell Assembly
- Stacking or Winding: The anode, separator, and cathode are stacked or wound together in precise configurations to form the cell structure.
- Electrolyte Filling: The cell assembly is filled with electrolyte, allowing for ionic transport necessary for battery operation.
- Sealing: The assembly is sealed in a prismatic casing, typically using heat sealing or ultrasonic welding to ensure safety and prevent leakage.
4. Formation and Aging
- Formation Cycling: The assembled cells undergo initial charge and discharge cycles to activate the electrochemical materials and stabilize performance.
- Aging: Cells are aged under controlled conditions to verify performance consistency and identify potential defects.
5. Testing and Quality Control
- Performance Testing: Each cell is subjected to rigorous testing for capacity, internal resistance, and overall performance to ensure compliance with specifications.
- Safety Testing: Tests for thermal stability, short-circuit resistance, and overcharging are conducted to ensure the safety of the cells.
6. Final Packaging
- Approved cells are carefully packaged for shipment or integration into battery packs for various applications.
● Advantages of a Prismatic Cell Production Line
1. Efficiency: Automation and streamlined processes reduce production time and increase throughput, essential for meeting growing demand for battery cells.
2. Consistency and Quality: Automated systems ensure uniformity in the manufacturing process, leading to higher quality and reliability of the finished cells.
3. Flexibility: Production lines can often be adjusted to accommodate different cell sizes and configurations, allowing for tailored solutions based on market needs.
4. Safety Enhancements: Built-in safety features help minimize risks associated with handling lithium-ion materials, ensuring compliance with industry standards.
● Applications of Prismatic Cells
- Electric Vehicles (EVs): Widely used in EV battery systems due to their high energy density and compact design.
- Energy Storage Systems: Employed in grid storage, renewable energy applications, and backup power solutions, providing reliable energy management.
- Consumer Electronics: Found in devices such as laptops and smartphones, where space and weight considerations are critical.
● Considerations for Prismatic Cell Production Lines
1. Material Compatibility: Ensuring that all materials used in the production process are compatible is crucial for optimal performance and safety.
2. Operator Training: Personnel must be trained to operate and maintain the production line to ensure smooth operation and compliance with safety standards.
3. Maintenance Requirements: Regular maintenance is essential to keep the production line running efficiently and to prevent downtime.
● Conclusion
A prismatic cell production line is a vital component in the manufacturing of high-performance lithium-ion battery cells. By integrating advanced technologies and streamlined processes, these production lines enhance efficiency, quality, and safety in battery manufacturing. As the demand for energy storage solutions continues to rise, the importance of prismatic cell production lines will grow, playing a crucial role in the transition to sustainable energy systems.
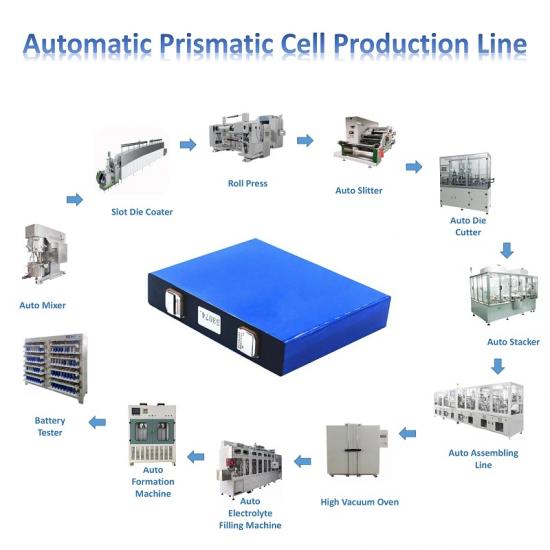